Materials
Retaining historic materials in lieu of replacement or covering helps achieve three goals—preserve the integrity of the building, maintain the character, and reduce environmental impacts. |
2.1 Historic building materials should not be removed, especially if in good condition.
a. Only repair damaged portions of the material using in kind materials that duplicate the size, shape and texture as closely as possible.
b. Remove non-historic materials if they have not achieved historic significance, making sure to test a small area to ensure the underlaying material will not be damaged.
c. If salvaging the original material to reuse as a structural member is not feasible, it should be salvaged as a cladding to replicate the original appearance of the material, while concealing the new structural treatment.
The wood siding above should be repaired with in-kind siding on the lower boards, however the upper boards in better condition should be sanded and repainted.
|

The example to the left shows a rounded column exposed to reveal the true 4x4 structural post supporting the front porch. Alterations that require new structural reinforcement should replicate the original column surround.
|
2.1 Preventative measures should be taken to ensure the long-term maintenance of historic materials.
a. Non-historic surface treatments, such as water-repellent coatings, may be applied to masonry as a last resort only after repointing and if masonry repairs have failed to arrest water penetration problems. Depending on the type of coating and the type of wall assembly it is being applied to it can have issues bonding properly, be challenging to remove, or create more water issues.
b. Applying water-repellent coatings that change the historic appearance or trap moisture and is not sufficiently permeable is not recommended.
c. Permeable, anti-graffiti coatings may be applied when appropriate.
d. Non-historic coatings, such as stucco, should not be applied to buildings as a substitute.
e. Chemical preservatives or paint may be applied to wood features that are subject to weathering, such as exposed beam ends, outriggers, or rafter tails and to exposed metals.

An example of a brick structure once covered in stucco that is failing and breaking away. In this case, the stucco should be carefully removed and the brick and mortar repaired.
|
2.3 Materials should only be cleaned when necessary to halt deterioration or remove heavy soiling or corrosion, not to create a “like-new” appearance which needlessly introduces chemicals or moisture into historic materials.
a. Cleaning tests on a small, inconspicuous portion of the building, should be conducted and be monitored over a sufficient period to allow long-range effects to be predicted and confirm no damage to the color, texture, or finish will result from the cleaning.
b. The gentlest method possible, such as using a low-pressure (300 psi) water and detergent and natural bristle or other soft-bristle brush should be used. Sandblasting and high-pressure water is not recommended as it will damage the material.
c. Water or liquid treatments should not be used when freezing temperatures are possible.
d. Chemicals that have the potential to damage such as acid on limestone or marble or failing to neutralize or rinse off chemical cleaners from the surface is discouraged.
Masonry
2.4 Masonry should be patched, spliced, consolidated, or otherwise reinforced using recognized preservation methods.
a. Repair may include the limited replacement in kind or with a compatible substitute material of those extensively deteriorated or missing parts of masonry features when there are surviving prototypes, such as terra-cotta brackets or stone balusters.
The example above should be avoided as the repair and replacement of brick over time has used three different bricks along with painted brick creating a mismatched appearance.
|
2.5 Mortar joints should be repointed where there is evidence of deterioration, such as disintegrating mortar, cracks in mortar joints, loose bricks, or damaged plaster on the interior.
a. Deteriorated lime mortar should be hand raked to avoid damaging the masonry.
b. Use of power tools only on horizontal joints on brick masonry in conjunction with hand chiseling to remove hard mortar that is deteriorated or that is a non-historic material which is causing damage to the masonry units. Mechanical tools should be used only by skilled masons in limited circumstances and generally not on short, vertical joints in brick masonry.
c. Historic mortar should be duplicated in strength, composition, color, and texture when repointing is necessary. In some cases, a lime- based mortar may also be considered when repointing Portland cement mortar because it is more flexible. Width and profile should also be duplicated. The best way to inform the proper mortar is through a mortar test of the existing mortar.
2.6 Brick that has never been painted should remain unpainted. Painting brick facades does not allow brick to breath as it was designed to do and will lead to issues with trapped moisture creating ongoing maintenance issues.
Stucco
2.7 Repair should be done by removing the damaged material and patching with new stucco that duplicates the old in strength, composition, color, and texture.
a. Deteriorated stucco should not be replaced with synthetic stucco, an exterior finish and insulation system (EFIS), cement board, or other non-traditional materials.
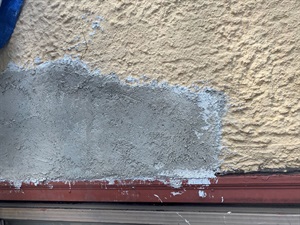
The image above shows a proper patch for an original stucco wall just before painting.
|
Wood
2.8 Paint removal should be considered only when there is paint surface deterioration and as part of an overall maintenance program which involves repainting or applying other appropriate coatings.
a. When paint is removed, it should be to the next sound layer using the gentles method possible (ex: hand scraping and hand sanding) prior to repainting. Chemical strippers may supplement these methods, but caustic paint-removers should not be used. Additionally, abrasive methods such as open-flame torches, orbital sanders, and high-pressure water should also be avoided.
b. Thermal devices like infrared heaters may be used when total removal of paint is necessary, and all flammable debris is first removed.
c. When dealing with lead paint, removal methods should employ a poultice to which paint adheres or using coatings that encapsulate lead paint where the paint is not required to be removed to meet environmental regulations.
d. Colors should be appropriate to the historically painted wood features however color is not regulated by these design guidelines.
Lead Based Paint and Historic Preservation
There are different levels of historic treatments appropriate to different levels of building significance and condition. Controlling lead hazards in historic buildings is a balancing act between several important objectives: childhood health, economic feasibility, and historic preservation. For instance, abatement methods that permanently reduce lead hazards may have a more negative effect on the character of a historically significant home than interim controls. For homes of great historic significance, removing historic paint layers and their substrates can result in an irretrievable loss of materials and craftsmanship. Interim controls are more suitable as a long-term solution as long as the historic property is maintained in good condition. As deteriorated elements are repaired or replaced, much of the lead-based paint can be removed with appropriate methods. Retention of the maximum amount of historic material as possible is the goal, while providing a lead-safe housing unit.
For more information visit: https://www.hud.gov/sites/documents/LBPH-20.PDF
|
Metal
2.9 Do not place incompatible metals together without an appropriate separation material. If not properly treated, the less noble metal will be corroded such as copper’s corrosive effect on cast iron, steel, tin, and aluminum.
a. Preserve historic cast iron, steel, copper and other original materials used in columns, roofs, fences and decorative features.
b. Modern metal siding such as aluminum or steel are not recommended and should not be used to cover historic wood, stucco, or brick siding. (See Preservation Brief 8)

The oriel window clad in metal pictured above has not been properly maintained and is rusting as a result.
|
Alternative Materials
2.10 Repairs are preferred over replacement even if the repair is done with a synthetic material.
a. If maintenance and repair have not been successful, alternative materials may be necessary to ensure continued preservation of a historic structure. In some situations, such as in the case of a fire, original materials may be damaged beyond repair or are lost altogether.
2.11 There are several reasons why a substitute would be needed outlined below and discussed in more detail in NPS Brief 16. This recently updated document has a wealth of information to guide decisions relating to alternative material use.
a. Unavailability of historic materials
b. Unavailability of skilled artisans or historic craft techniques
c. Inadequate durability of original materials
d. Code-required performance changes
e. Replacement of secondary features
f. Reconstruction of a missing feature
g. Enhanced resilience and sustainability
2.12 It is not appropriate to cover up original materials if it will alter the appearance, proportions, and details of the historic building and if it will conceal future deterioration.
a. If a compelling reason is found to use alternative replacement materials, quality should be a primary concern when selecting the substitute material. Applications should include information on how the product has held up over time.
2.13 To ensure the replacement material is comparable to the original material the substitute should meet the following basic criteria:
a. The material is compatible with or replicates the historic material in appearance.
b. The physical properties are similar to the original material or it is installed in a manner that the old and new material do not create issues.
c. The material must meet basic performance expectations over an extended period, being comparable to the performance of the original material.
d. The level and location of the alternative material on the building will be considered. Preservation of the historic material at eye level is more important than areas higher up or on non-primary facades where it will be challenging to tell the difference between original and replacement.
Synthetic Products
2.14 While it is recommended to remove non-original materials during a project and restore the original material, existing non-original products such as vinyl or metal siding may be replaced with the same material administratively. The addition of new non-original siding to a building requires HPC review.
2.15 Vinyl and metal siding is not recommended as a new material on buildings because it does not allow an old house to breathe due to the unknown factor in moisture resistance in historic homes. Without proper air flow, wood siding underneath can start to rot and create perfect conditions for termites.
a. If vinyl siding is found to meet the alternative material criteria for a project, the profile shall match the width of the original siding.
b. Vinyl siding should not be used to cover up a stucco or masonry building.
2.16 Fiber cement products are comparable replacements for historic materials like asbestos siding that may need to be replaced for environmental concerns.
a. Widths and profile should match the original material profile.
b. If replacing or covering wood siding, a smooth finish should be selected over an imitation wood grain look.
Submission Requirements for Alternative Materials
To aid in review and ensure the substitute material meets the guidelines the following items need to be submitted with the application for a certificate:
- Pictures with dimensions of the historic material width and depth at various angles.
- Description with supporting pictures of the condition of the existing material and need for replacement.
- Description of the work done to date to try to maintain or repair the material.
- Information (brochures, cut sheets, samples, etc.) describing the proposed alternative material which includes dimensions, material composition, texture, installation method, and demonstrated long-term performance/durability.
|